High temperature ceramics draws attention of manufacturers due to specific properties and a broad range of application in different industries that require high temperatures.
Physicalproperties, hardness factor and stability at high temperatures put high temperature ceramics high for high temperature treatment of materials both in vacuum or without one.
Nevertheless, resistance to oxidation limited by 500ºC is considered one of the crucial disadvantages of this type. Contact with air can substantially affect its high temperature properties. This is the reason why high temperature ceramics is used in nodes isolated from air.
Refractory materials and high temperature ceramics across the globe is still an object of study though gained its pace among key structural materials in several industries, such as:
-
Metal work
-
Aviation
-
Rocketry
-
Nuclear energy
-
Electronics
-
Chemical industry
Silicon carbide ceramic products
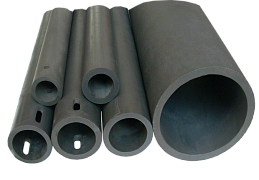
Silicon carbide (SiC) ceramics ensures high thermal resistance and high operational characteristics. Among the key benefits one can name resistance to temperature gradient, high corrosion resistance and stable dimensions.
Silicon carbide ceramics was widely adopted in automobile production and aerospace as abrasive semiconductor structural high temperature material for production of engine elements and thermal facilities, as well as other electronics.
Application:
- Fittings and structural elements of high temperature furnaces;
- Nozzles for various purposes, burner tops, retort vessels;
- Jackets for thermal couples, heat-resistive tubes;
- Crucibles, barrels, casings of different configuration;
- Friction couple;
- Heaters;
- Elements of thermal combustion facilities etc.
Benefits:
- High mechanical robustness;
- High hardness;
- Resistance to thermal shock;
- High durability when exposed to abrasive stress and high temperatures;
- Resistance to corrosion and oxidizing;
- High resistance to exposure of aggressive media;
- High electric conductivity;
- Low thermal expansion coefficient = high thermal resistance, stable geometry;
- High chemical resistance.
The “NPO “GKMP” LLC proposes silicon carbide ceramic parts of different design (SSiC, SiSiC, RSiC and OSiC) per Customer’s requirements.
Silicon infiltrated silicium carbide (SiSiC)
Operating temperature, 0С |
1380 |
Density, g/cm3 |
≥3.02 |
Apparent porosity, % |
≤0.1 |
Flexural strength, MPa |
250(20°С) 280 (1200°С) |
Elasticity modulus, GPa |
300(1200°С) 330(20°С) |
Thermal conductivity, W/m·K |
45(1200°С) |
Strength |
13 |
Resistance to acids and alkali |
high |
Sintered silicon carbide (SSiC)
Free silicon, % |
<0.1 |
Silicon carbide, % |
≥99 |
Poured density, g/cm3 |
3.1-3.15 |
Vickers hardness, НV |
2500 |
Rockwell hardness, НRA |
94 |
Open porosity, % |
<0.2 |
Compressive strength, MPa |
>3000 |
Flexural strength, MPa |
>400 |
Elasticity modulus, GPa |
410 |
Thermal conductivity, W/m·K |
100-120 |
Recrystallized silicon carbide (RSiC)
α- SiC, % |
98.5 |
Maximal operating temperature, oC |
1650 |
Porosity, % |
15 |
Poured density, g/cm3 |
2.60-2.74 |
Compressive strength, MPa |
>600 |
Flexural strength, MPa |
90-100 |
Young modulus, ГПа |
240 |
Thermal conductivity, W/m·K |
24 |
Oxide-bonded silicon carbide (OSiC)
SiC, % |
≥90 |
Maximal operating temperature, oC |
1550 |
Open porosity, % |
7-8 |
Poured density, g/cm3 |
2.75 |
Compressive strength, MPa |
≥1300 |
Tensile strength at ambient temperature , MPa |
≥500 |
Nitride-bonded Silicon carbide (NSiC)
SiC content, % |
≥75 |
Si3N4 content, % |
≥21 |
Fe2O3 content, % |
≤0.5 |
Maximal operating temperature, °С |
1550 |
Porosity, % |
≤15 |
Density, g/cm3 |
2.6-2.7 |
Flexural strength, MPa |
≥180 |
Flexural strength (20°С), MPa |
≥45 |
Flexural strength (1200°С), MPa |
≥50 |
Thermal conductivity (800°С), W/m·K |
≥18 |
Thermal conductivity (1200°С), W/m·K |
≥14 |
The “NPO “GKMP” LLC proposes silicon carbide ceramic parts of different design (SSiC, SiSiC, RSiC and OSiC) per Customer’s drawing and dimensions required.
Zirconium dioxide ceramics
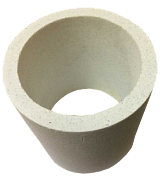
Products made of zirconium dioxide technical ceramics are chemically inert (do not react with aggressive agents).
Zirconium dioxide (ZrO2) has a unique set of properties, such as:
- High hardness;
- Perfect corrosion resistance;
- Low thermal conductivity;
- Crack resistance;
- Robustness at high temperatures.
The combination of these properties renders Zirconium dioxide ceramics irreplaceable for numerous industries (from high resistive parts to medicine).
Zirconium dioxide is used to obtain extra heat resistive products, heat resistive enamel, refractory glass, different types of ceramics, ceramic pigments, thermal protective coatings, catalyzers, cutters and abrasive materials. Recently zirconium dioxide is widely used in fiber optics and production of ceramics to be integrated in electronic devices.
Characteristics:
- Maintain robustness at high temperatures (melting point 2715 °С);
- High hardness;
- Corrosion resistance;
- Low thermal conductivity.
Application:
We supply zirconium dioxide products of different design per Customer’s individual drawings.
Basic properties of the material ZrO2 95%+ Y2O3 5%
Density, g/cm3 |
6.03 |
Open porosity, % |
0 |
Vickers hardness |
1150 (HV0.5) |
Elasticity modulus, GPa |
205 |
Flexural strength, MPa |
1300 |
Compressive strength, MPa |
3000 |
Thermal conductivity at 20-100°С, W/mK |
2.0 |
Thermal resistance |
280 (△ T °С) |
Linear thermal expansion coefficient at 20-1000°С, 10-6К-1 |
10-11 |
Volumetric specific resistance (20°С) |
≥1010 (Ω) |
Maximal operating temperature |
1000 |
Material can be used with alternative percentage ZrO2 + Y2O3.
It is possible to use calcium oxide or magnesium oxide as stabilizer, if so requested by the Customer.
The “NPO “GKMP” LLC supplies zirconium dioxide products of different design per Customer’s individual drawings.
Aluminium oxide ceramics
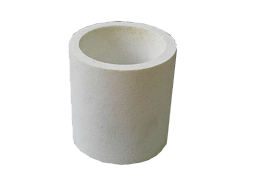
Key properties of aluminum oxide (Al2O3):
- High hardness;
- High thermal conductivity;
- High corrosion resistance;
- Low density;
- Robustness at high temperatures;
- Electric insulation properties;
- Low cost in comparison with other ceramic materials
The main areas of use from corundum (aluminum oxide):
- Facing of consumable hardware;
- End seal rings;
- Drain bushings, wiring, guiding beams;
- Roller balls;
- Milling fittings;
- Burners;
- Crucibles;
- Valve components and shut-offs;
- Nozzles for argon arc welding machines;
- Electric insulators;
There are few modifications of aluminum oxide depending on the main phase of impurities that differ in strength and chemical stability.
Al2O3, % | 60 | 75 | 80 | 85 | 92 | 95 | 99 | 99.7 |
Density, g/cm3 |
3.0 |
3.1 |
3.3 |
3.4 |
3.6 |
3.7 |
3.81 |
3.85 |
Flexural strength, MPa |
205 |
280 |
215.7 |
230 |
312 |
304 |
340 |
370 |
Linear thermal expansion coefficient, (25-800оС), 10-6/оС |
7.1 |
7.6 |
7.6 |
7.6 |
7.5 |
7.3 |
7.6 |
7.6 |
Dielectric strength, kW/mm |
10 |
10 |
10 |
10 |
10 |
10 |
10 |
10 |
Specific electric resistance 20°С ,Ω•сm 300°С,Ω•сm |
>1014 >1013 |
>1014 >1013 |
>1014 >1013 |
>1014 >1013 |
>1014 >1013 |
>1014 >1012 |
>1014 >1010 |
>1014 >1010 |
Operating temperature, оС |
1350 |
1000 |
1250 |
1290 |
1390 |
1480 |
1600 |
1700 |
Mohs hardness |
7.5 |
7.5 |
7.5 |
7.5 |
8.5 |
8.8 |
9.0 |
9.0 |
Heat resistance, оС |
1800 |
1700 |
1800 |
1850 |
1920 |
2000 |
2030 |
2040 |
ZTA based ceramics
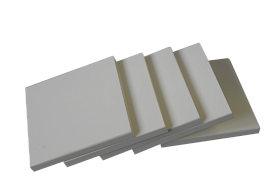
ZTA is a combination of alumina and 10-20% zirconium
ZTA properties:
- Additional hardness and viscosity compared to that of aluminum oxide;
- Better price that that of zirconium dioxide;
- High corrosion resistance;
- High fracture viscosity;
- High flexural strength.
Application:
- Insulators, sensors, piston bushings and pump components;
- Liquid supply system components;
- LED chip carriers.
The main characteristics of the material:
ZrO, % |
20 |
Al2O3+ZrO2, % |
30 |
Density, g/cm3 |
≥4.00 |
Water absorbed, % |
0 |
Hardness, HV(GPa) |
1650 |
Flexural strength, MPa |
400-500 |
Compression strength, MPa |
2800 |
Fracture viscosity, MPa m3/2 |
9.8 |
Elasticity modulus, GPa |
310 |
Maximal operating temperature, оС |
1450 |
Sintering temperature, оС |
1650 |
Thermal expansion coefficient, X10-6/oC |
8.2 |
Thermal conductivity, W/m • K(25-300°С) |
9.8 |
- The “NPO “GKMP” LLC supplies ZTA products of different design per Customer’s individual drawings.
- Maximal operating temperature of ZTA products - 1450°С. ZTA is often used to produce insulators, sensors and pump components, fluid supply system components, casing and LED chips carriers.
Boron nitride ceramics
Boron nitride ceramics product (BN)
Boron nitride products are widely used in high temperature hardware.
One of the key characteristics of boron nitride is that it provides to any item more thermal resistance, density and stability. Boron nitride is widely used in heavy industry and for chemicals.
Boron nitride ceramics was widely adopted in aircraft and rocket engineering, machinery and glass melting, chemical industry, energy and metallurgy. Production of high temperature hardware often involves crucibles, insulators and electric vacuum tools of boron nitride.
A unique combination of thermal, physical and chemical characteristics of boron nitride ceramics make it perfect to meet complex needs and tackle the entire range of production challenges.
Application:
- Crucibles, insulators and high temperature ceramics;
- High temperature lubricants;
- Synthesis of extra-soil substances;
- Production of electric vacuum hardware and semiconductors.
Boron nitride: HEXAGONAL (α) — h-BN, (white graphite, talc-like powder, has a hexagonal crystal structure and semiconductor properties).
Characteristics:
- Thermal capacity;
- Non-toxic;
- Chemical inertness;
- High dielectric strength;
- Low dielectric capacity.
We supply heat resistive ceramics based on hexagonal boron nitride (of different shapes and dimensions per Customer’s needs and requirements).
Hot-pressed hexagonal boron nitride (BN)
Composition | BN˃99% | BN˃98% | BN+SiC+ZrO2 | BN+AlN |
Binder |
Self-binding |
B2O3 |
AlBO3 |
AlBO3 |
Density, g/cm3 |
1.9-2.0 |
2.1-2.2 |
2.3-3.0 |
2.5-2.6 |
Specific resistance (at 25°C), Ω/cm |
>1014 |
˃1013 |
˃1012 |
˃1014 |
Maximal operating temperature, Oxidizer, °С |
900 |
900 |
900 |
900 |
Maximal operating temperature, Inert gas , °С |
2300 |
2000 |
1700 |
1700 |
Maximal operating temperature, High vacuum, °С |
1800 |
1800 |
1700 |
1700 |
Flexural strength, MPa |
25 |
75 |
100 |
130 |
Compressive strength, MPa |
100 |
100 |
300 |
250 |
Thermal expansion coefficient 25-1000°C, 10-6/K |
0-2 |
2.0 |
4.0 |
4.5 |
Thermal conductivity, W/mK |
50 |
30 |
40 |
60 |
We produce thermal resistive ceramics based on hexagonal boron nitride of different shapes and dimensions per Customer’s needs and requirements.
Pyrolytic boron nitride ceramics (p-bn)
Boron nitride ceramics is widely used in production of high temperature hardware. One of the key characteristics of boron nitride is that this component provides heat resistance, density and stability to any piece.
Boron nitride ceramics was widely adopted in aircraft and rocket engineering, machinery and glass melting, chemical industry, energy and metallurgy. Production of high temperature hardware often involves crucibles, insulators and electric vacuum tools of boron nitride.
A unique combination of thermal, physical and chemical characteristics of boron nitride ceramics make it perfect to meet complex needs and tackle the entire range of production challenges.
Pyrolytic boron nitride is obtained via gas and phase chemical deposition. Compared to standard composition of boron nitride, pyrolytic boron nitride is much purer and has a number of benefits.
Application:
- High vacuum processes (as material for crucibles, baths, tubes and vessels etc.);
- Crystal growing processes (incl., semiconductor crystals);
- Molecular beam epitaxy;
- Special-purpose hardware and electronics (production of integral micro circuits, UHF-energy output displays, etc.);
- Synthesis and growing of semiconductors.
Characteristics:
- High purity (˃99.99%);
- High thermal resistance;
- Chemical inertness;
- High thermal conductivity;
- Radio transparency;
- Non-toxic.
We supply pyrolytic boron nitride ceramics of different shapes and dimensions per Customer’s needs and requirements.
Pyrolytic boron nitride (p-BN)
Density, g/cm3 |
1.95-2.20 |
Crystallic grid constant, µm |
a: 2.504*10-10 c:6.692*10-10 |
Specific resistance, Ω/cm |
3.11*1011 |
Flexural strength (ab), N/mm2 |
153.86 |
Flexural strength, N/mm2 c ab |
243.63 197.76 |
Elasticity coefficient, N/mm2 |
235690 |
Thermal conductivity , 200, W/m·K |
a:60 c:2.6 |
Thermal conductivity , 900, W/m·K |
a:43.7 c:2.8 |
Dielectric strength (at ambient temperature), kW/mm |
56 |
The “NPO “GKMP” LLC supplies a wide range of thermal resistive ceramics based on pyrolytic boron nitride (of different shapes and dimensions per Customer’s needs and requirements).