Leakage check and gas analysis

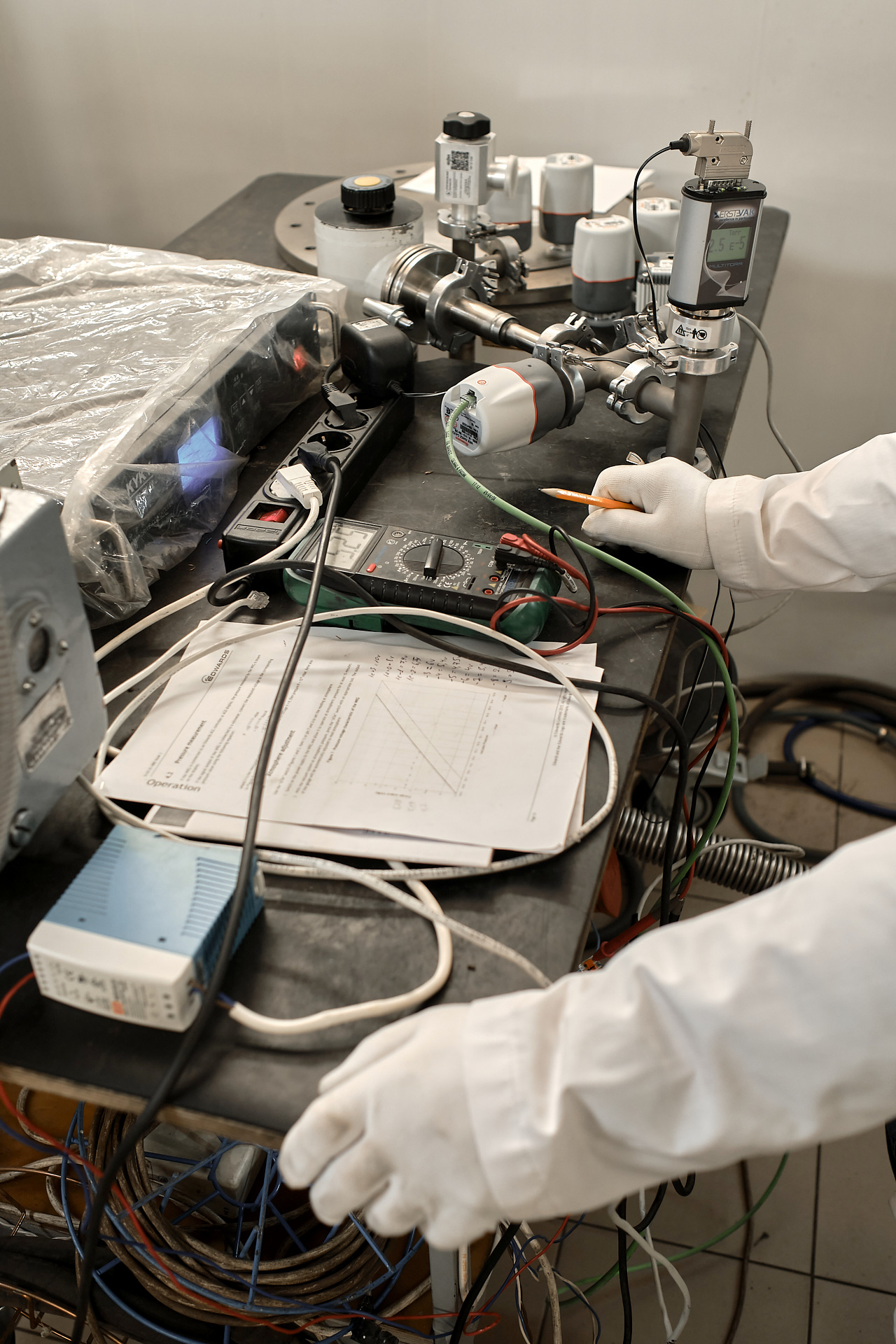
The production capacities comprise a quality assurance that has a dedicated internal laboratory equipped with the hardware required to perform the following quality research.
The welded seams are subject to X-ray quality inspection. The vacuum integrity of welded seams and vacuum volumes are checked with the help of brand-new helium leak detectors produced by the leading manufacturers. Linear and angle values, surface roughness, hardness, surface thickness and electric values are well maintained and controlled.
The staff engaged in operations at production sites and in laboratories is properly trained and certified by the NACWP Rosatom and ISO standards.
Laboratory equipment
- Upgraded Pull tests machine P-50
- Mass-spectrometer Leybold Phoenix QuatroDry
- X-ray machine RPD-200
- Computer radiography facility Phosphomatic-40/100
- X-ray machine ARSENAL 160 HC
- Optical and emission spectrometer for chemical analysis DFS-500
- Ultrasonic fault detector UCD50
- Mass-spectrometric leak detector
- Absolute laser tracker ATR960-MR
Project implementation
- Acceptance
- Rating
- Analysis
- The deal
- Preparation
- The process
- Delivery
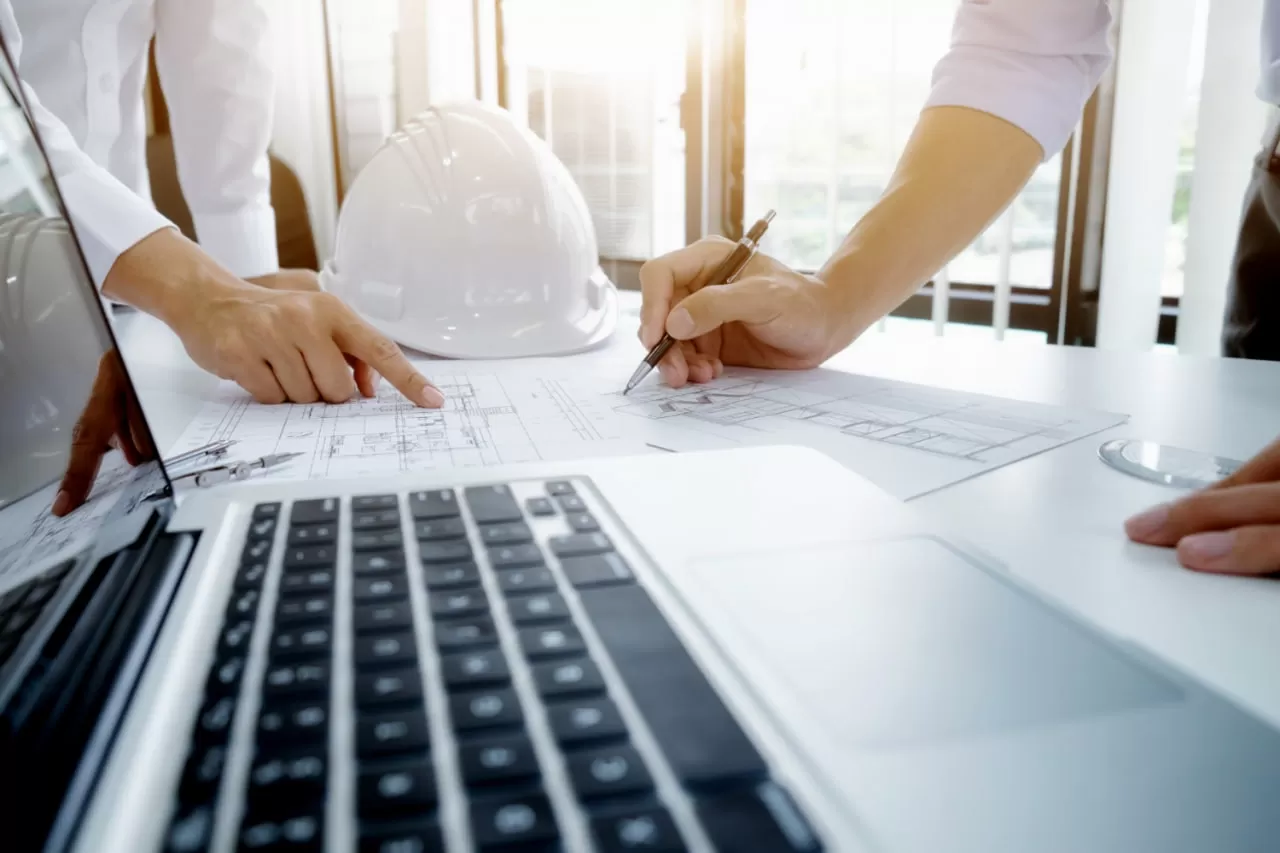
Acceptance and evaluation: at this stage all materials and hardware necessary for further implementation of the project are accepted. Moreover, quality and conformity assessment is made to make sure that the project is in line with requirements.
Analysis and transaction: this stage covers analysis of all data and materials, as well as transactions and agreements to be entered into between suppliers and contractors.
Preparation and production flow: this stage includes preparation of all required documents and schedules related to the project. The released product or services rendered shall be in accordance with the requirements of the project.
Commissioning and completion of the project: at the last stage the project is handed over to the customer, the works performed are subject to quality inspection, possible defects are rectified, if any. After that the project is considered completed and ready for use.
Non-destructive testing
Ultrasonic control
This method uses ultrasonic waves to inspect material and detect different defects, for example cracks, pores, inclusions and other imperfections. This method can also be used to check the quality of welded seams, riveted connections and other complex pieces.
Mass-spectrometric control
This method can be used to check cleanliness of materials, to detect impurities and analyze molecular structure. One of the main benefits of the mass-spectrometric method is its high accuracy and sensibility. This method detects even the tiniest amounts of impurities in materials.
Radiographic control
Used to detect defects of metallic structures, for example welded seams. This method is based on X-rays or gamma radiation to capture images of inner structures of the object. Radiographic control enables to detect such defects like cracks, porosity, poor penetration and others that can lead to the loss of structure.
Dye-penetrant inspection
This quality control method has a number of advantages in comparison with others. Firstly, it enables to detect defects at early stage, prevent their propagation and improve the product quality. Secondly, dye-penetrant inspection is a quick and simple method that does not require any special hardware or suspension in production. Thirdly, this method enables to control product quality in real time and optimizes costs imposed by quality assurances.
Visual control and measurements
Visual control enables to inspect appearance of the item produced, detect visible defects and define its conformity with requirements. Measurement of the item’s dimensions is aimed at control of its geometry and ensure the proper accuracy. These control methods are quick and simple but rather precise; they can be used both separately or in combination with other quality control methods.
Laboratory test
To define mechanical properties of metals and welded seams (tensile strength, yield, elongation and narrowing ratio, shock viscosity, hardness)
To define the chemical composition of metals, brand of the material used, welding rod and X-ray fluorescent and spectral analysis
Metallographic inspection of metal structure and welded seams
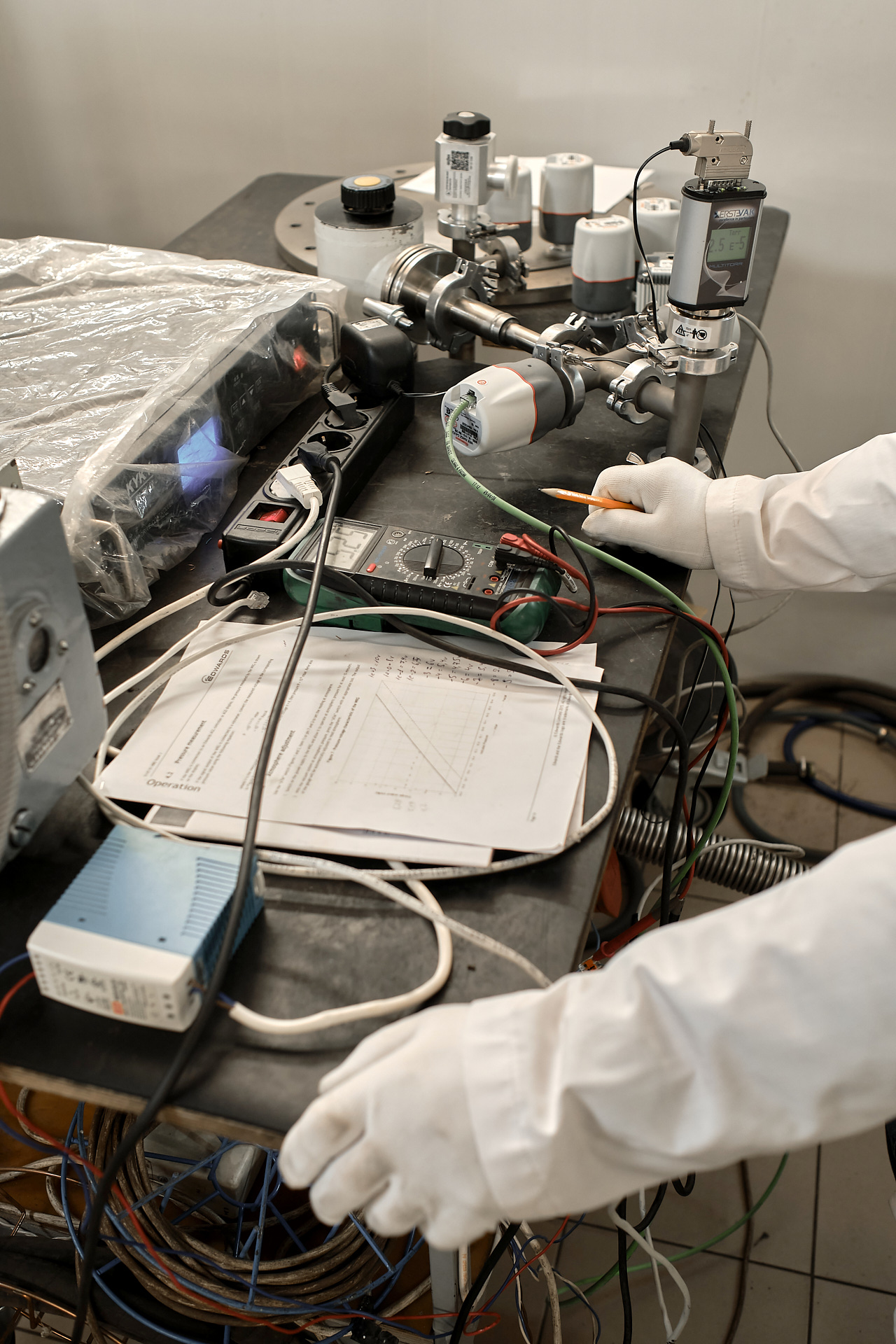
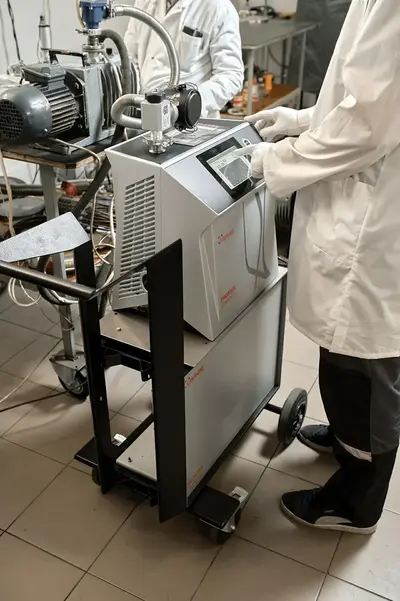