Blanking operations
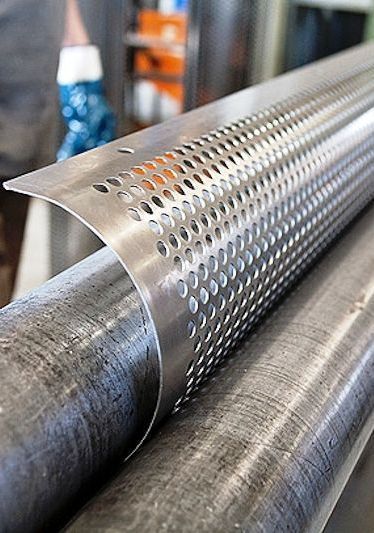
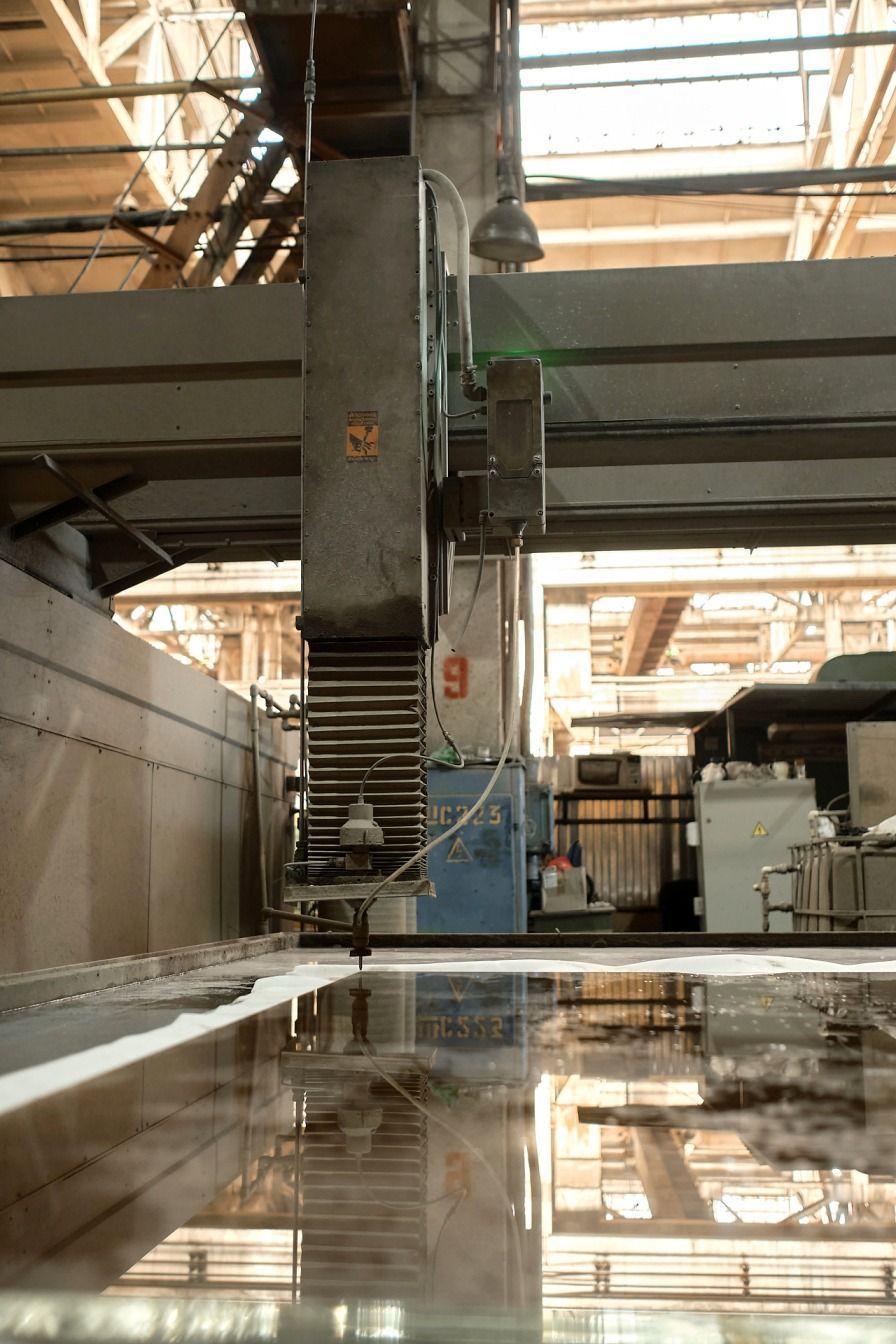
Production equipment and machines
Types of metal processing
Gas-oxygen cutting
Sheet thickness, mm
6-200
CNC dimensions, mm
1800*6000
While cutting oxygen reacts with heated metal thus imposing its oxidation and instant combustion. Oxides of fused metal are blown from the cutting area. This method is crucial for large-sized workpieces, heavy plates or large diameter tubes. It ensures stable burning of large-sized pieces in cross-section and high-quality cutting.
Plasma cutting
Sheet thickness, mm
32
CNC dimensions, mm
2000*6000
Plasma cutting uses plasma beam as cutting material. High speed gases blow off the melted metal. This method allows to cut any metal including the most refractory ones, has a quite high cutting speed and ensures high quality with a saw-cut smaller than that of the gas cutting.
Hydro-abrasive cutting
Sheet thickness, mm
300
CNC dimensions, mm
2750*4450
Hydro-abrasive cutting uses water jet as a cutting tool to cut metal with high speed and at high pressure. Sand is used as an abrasive. This method allows cutting of heavy plates. No high temperature while cutting makes the process free from any bead welds to be dealt with. Hydro-abrasive cutting is fit to cut almost any metal.
Guillotine shear cutting
Sheet thickness, mm
32
Sheet width, mm
3150
Rolled steel, diameter mm
40
Guillotine shear cutting is used to cut rolled metal sheets from one edge to another. The machine is based on slash movement of a flat slanted knife. The key advantage of guillotine tool is the speed cutting of workpieces.
Bending
Tube diameter mm
5-63
Wall thickness, not to exceed, mm
4
Our company perform sroll-bending of sheet and profiled metal in cold condition using CNC machines with force up to 220 tons.
3-roller bending
Sheetsize, mm
16*2000
Minimal bend radius, mm
240
This method enables to produce pieces with small bend radius and high precision of shape. 3-roller bending can be used to manufacture tubes, profiles and other items made of rolled metal.
Band saw cutting
Maximal diameter, mm
380*500
Band saw cutting is carried out using a special machine. This is one of the most efficient method of metal machining: the cutting is done via a band saw blade embedded into the body of the machine. The machining is highly precise and provides a perfect saw-cut quality.
Forging
Force, t
1600
Dimensions, mm
1140*1240
Forging is an intermediate preparatory machining of a workpiece by hammering. The latter is carried out by hammers and presses with self-guiding dies up to 100 kg. As a result, we produce a piece of an average complexity. Despite the fact that this process is not that much efficient, it is considered as cost saving and justified.
Project implementation
- Acceptance
- Rating
- Analysis
- The deal
- Preparation
- The process
- Delivery
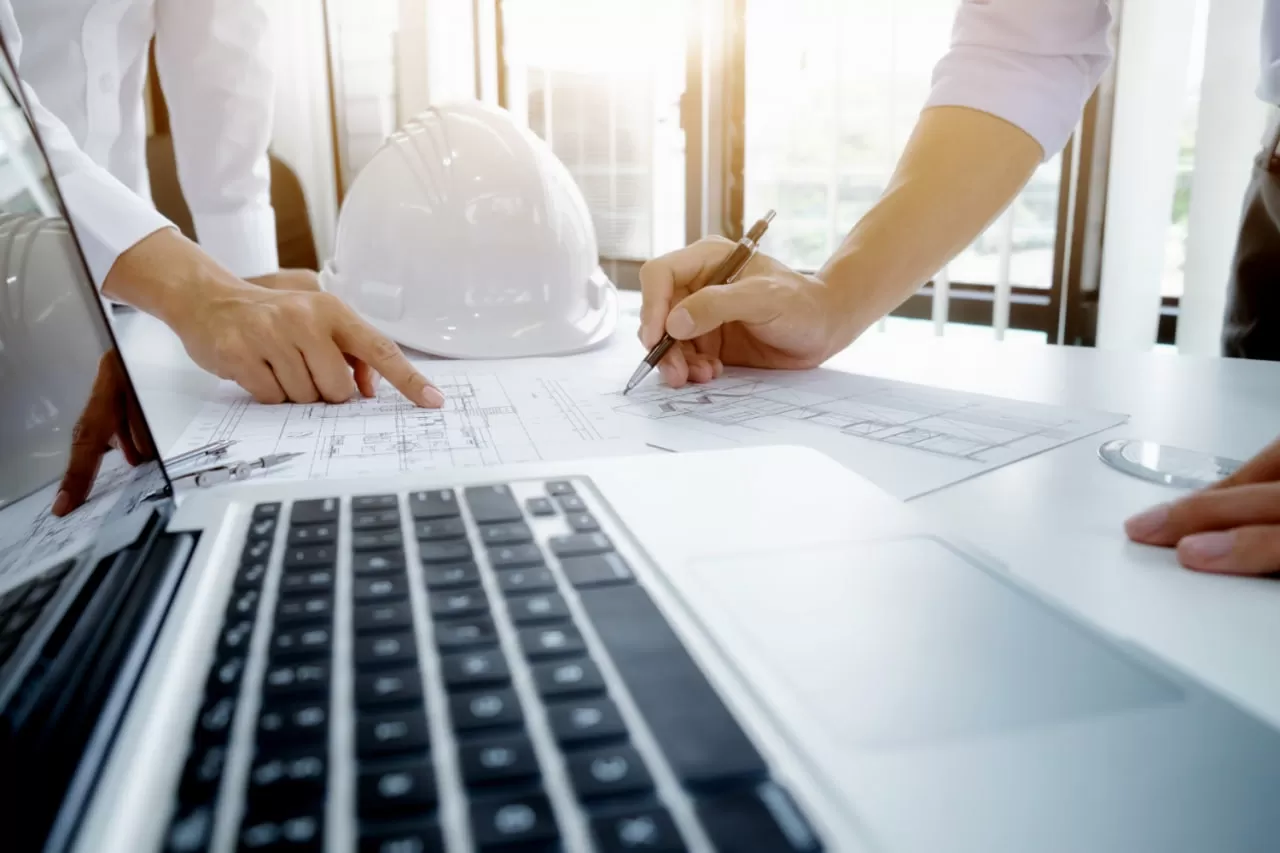
Acceptance and evaluation: at this stage all materials and hardware necessary for further implementation of the project are accepted. Moreover, quality and conformity assessment is made to make sure that the project is in line with requirements.
Analysis and transaction: this stage covers analysis of all data and materials, as well as transactions and agreements to be entered into between suppliers and contractors.
Preparation and production flow: this stage includes preparation of all required documents and schedules related to the project. The released product or services rendered shall be in accordance with the requirements of the project.
Commissioning and completion of the project: at the last stage the project is handed over to the customer, the works performed are subject to quality inspection, possible defects are rectified, if any. After that the project is considered completed and ready for use.
Details about the service
Blanking operations are part of the key technological processes. They represent the initial preforming process of a workpiece, i.e. the first stage in production of an end item. One of the main steps in preforming is the metal cutting followed by bending and forging. The main purpose of blanking operations is to give a required shape to the workpiece, ensure its dimensions and quality to be checked at later stages of machining.
All these measures are anticipated to provide accuracy and quality of an end item. Once blanking operations are completed, the workpiece is subject to quality inspection to verify the shape, dimensions, surface quality, and to detect any possible defects of machining. In any faults are detected, the workpiece undergoes additional machining; should the defects detected be irreparable, the workpiece is scraped.
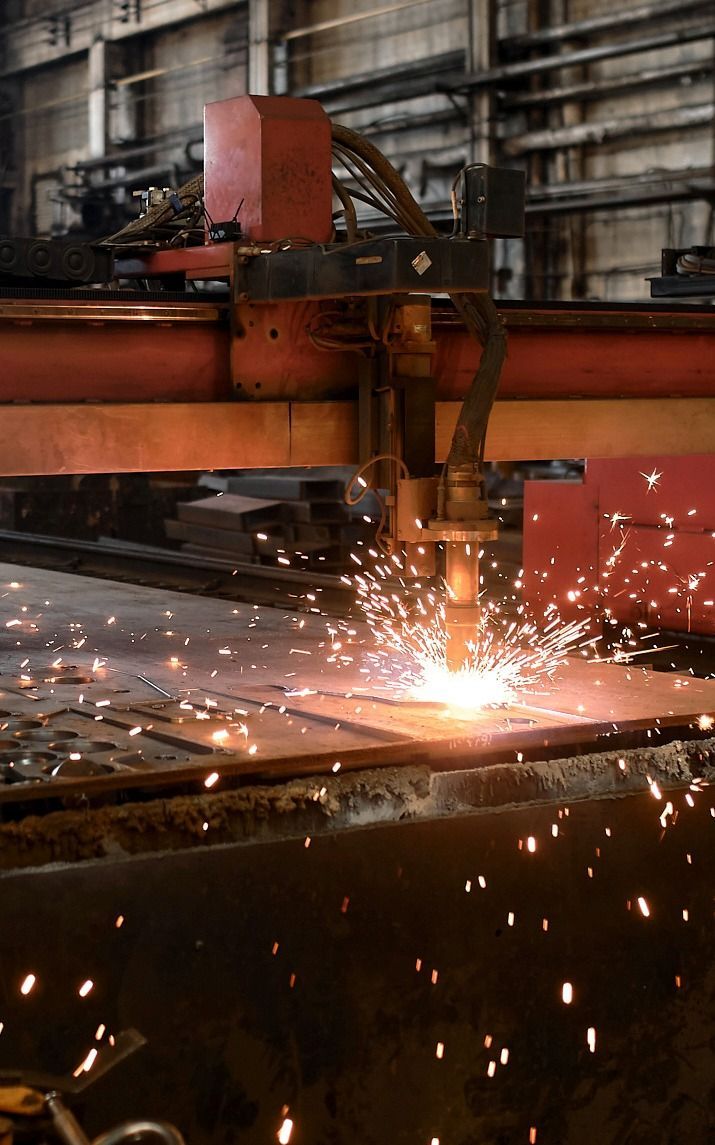