Machining
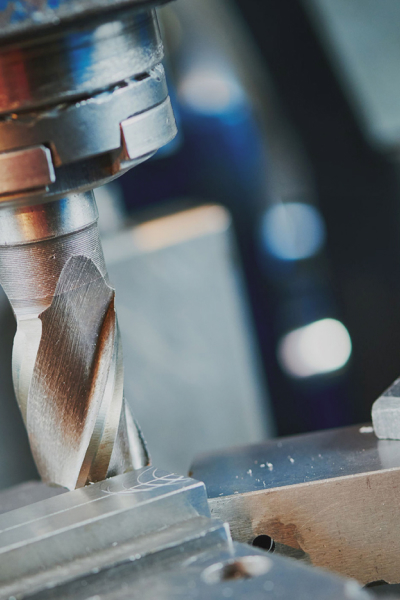
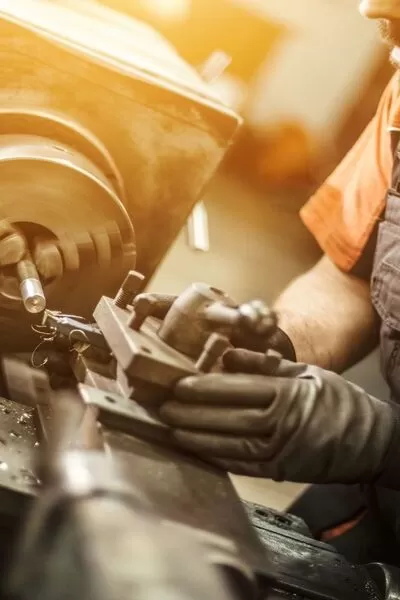
Our company performs machining of metallic parts for production purposes. We implement comprehensive milling, turning and forming operations of fine tolerances thus ensuring high quality surface.
All works are made using the cutting-edge high-precision hardware by qualified operators. CNC machines minimize human factor and enable to perform machining of metal pieces both per GOST and per Customers drawings and drafts.
If you have any metal pieces for industrial equipment to be machined, we are ready to provide our best proposal and assist you in implementation of your products.
Production equipment and machines
Types of metal processing
Lathe machining
Maximal diameter of a workpiece, mm
1000
Maximal length of the workpiece, mm
5000
Lathe machining of a workpiece removes a thin metallic layer from a metal workpiece in order to have a piece of required shape and surface roughness. Our production capacities have advanced lathe CNC machines that ensure the required quality of lathe work, integrity and high metal cutting speed. A wide variety of applications make it possible to produce pieces of any shape.
Boring machining
Maximal diameter of a workpiece, mm
2500
Maximal length of the workpiece, mm
2000
Boring lathe machining is used to machine large-sized workpieces. Relatively high machining speed and operating mode of a boring lathe machine – a vertical rotation axis of the spindle produces complex-shaped and the most “inconvenient” workpieces, as well as those of large diameter.
Milling/boring
Max. dimensions, mm
3000*3000*2500
Milling enables to create complex shapes and holes, and boring process is intended to expand and deepen already existing ones. Both methods provide high accuracy and repeatability of machining.
Planing
Dimensions, mm
1250*1120*4000
This technique is used to remove material layers from the surface of a workpiece. It requires high precision and ensures minimal roughness, required geometry and dimension of a workpiece. Thanks to planing technique one can reach the required dimensions and shape with the minimal tolerance. This method ensures high precision of assembly and substantial lifetime of an end item.
Surface grinding
Surface dimensions, mm
1250*320*400
Maximal weight, kg
600
Cylindric grinding: Maximal diameter, mm
400
Maximal length, mm
2000
Grinding is the most common metal finishing machining method that ensures homogenous removal of material and protects the surface from grooves and scratches. It also provides the highest accuracy and quality of the product, ensures the proper roughness. Grinding process eliminates defects and improves bonding of the subsequent coating with grinded surface of a workpiece.
Internal grinding
Maximal diameter of a workpiece, mm
800
Maximal length of a workpiece, mm
630
Maximal diameter of holes, mm
500
Maximal length of holes, mm
500
Internal grinding is used to machine cylindric, conic and irregularly shapes holes. Integral grinding can be used to machine even long length pieces.
Gear machining
Maximal diameter while cutting conical and radial turbines, mm
2000
Gear module, mm
20
Configuration
straight
slanted
herringbone
circular
Gear machining is a widely used production and machining method for cogwheels and other similar pieces. Our company has vast capacities to manufacture conical and radial wheels of large diameter and various configuration.
Beading
Maximal metal thickness, mm
2
Maximal distance from sheet edge, mm
750
Diameter of machined tube, mm
200-1025
This machining method generates a specific texturized pattern on the surface. Therefore, the structure of the end item is equipped with additional reinforcement ribs that improve strength, service life and decrease sweep effect of the surface. Coupling profiles made in course of beading enhance the strength of metallic structures and edges of different metallic parts.
Project implementation
- Acceptance
- Rating
- Analysis
- The deal
- Preparation
- The process
- Delivery
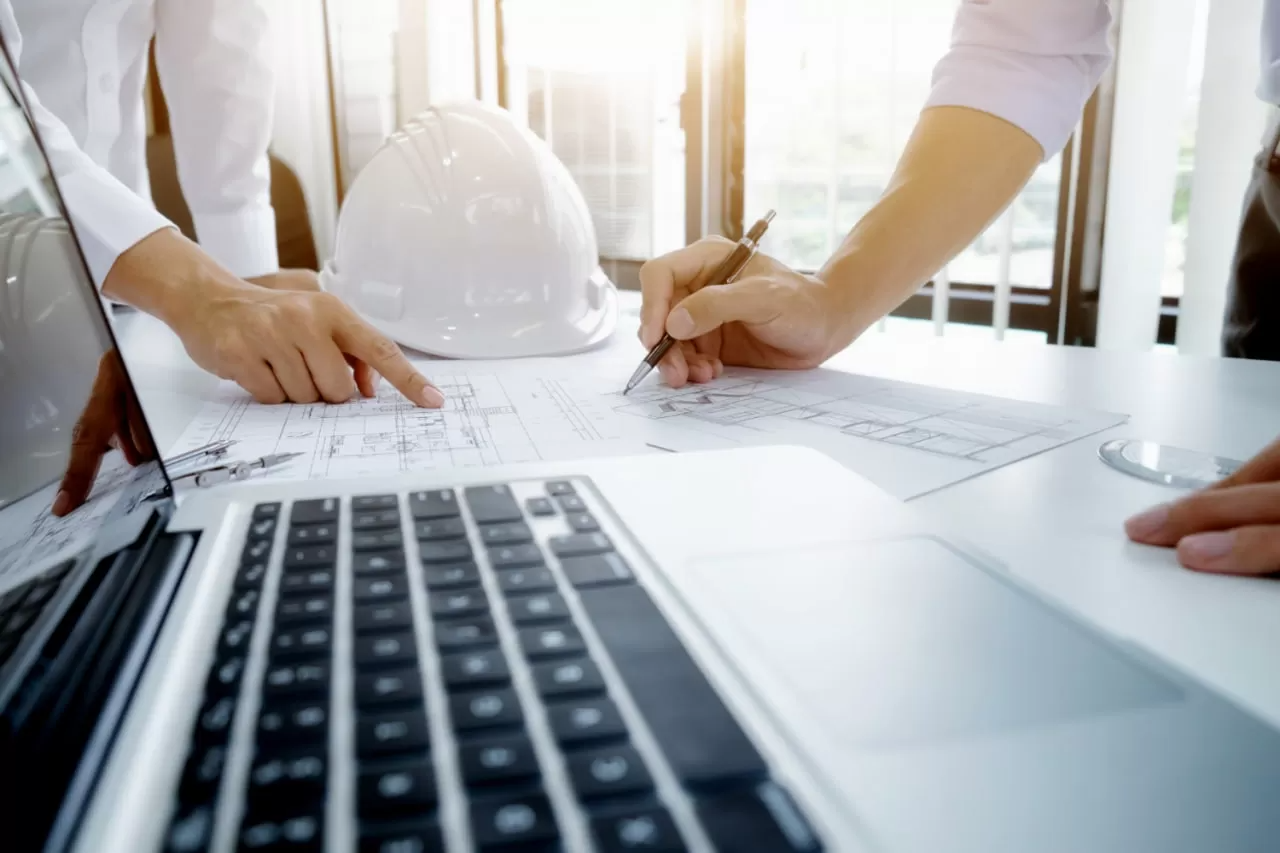
Acceptance of a machining assignment starts when the Customer submits the drawing or technical specification to manufacture a piece. Then an operator performs an analysis of the assignment and estimates complexity and scope of works, required hardware and materials.
This procedure is followed by a dedicate estimate enlisting lead time, cost and required resources. if the customer agrees with conditions, an После этого составляется смета на выполнение задания, a contract for works envisaged is made.
After that a work place is prepared and required tools and materials for metal machining are selected. Then one actually starts machining of a piece that may include milling, lathe, drilling, grinding and other operations.
Read more
General description
Machining is a processing of workpieces in order to give them required shape and dimensions, as well as to meet the required quality of the surface via different technological processes of metal machining.
Machining removes material layer from the surface of a workpiece in a single or few pass. Different tools and technological processes can be applied to machine different surfaces, depending on complexity of the structure, production accuracy and quality of the surface. The allowance diminishes from one machining to another, thus increasing the accuracy and cleanliness of the surface.
One of the main benefits of machining is the possibility to produce high-precision pieces with substantial repeatability. This feature is vital for production of highly refined mechanisms and devices where even a minor deviation can lead to serious consequences.
Moreover, machining can alter the shape and dimensions of metallic parts per Customer’s requirements. Therefore, parts of any shape and dimensions can be produced to meet the needs of numerous industries.
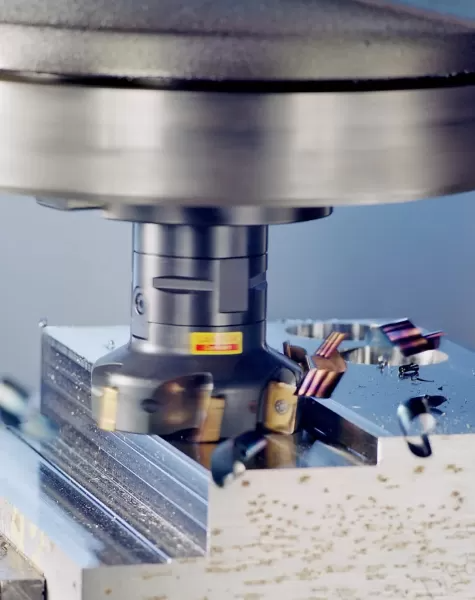